Glossary
Glossary for plastics and each coating technologies.
Plastic
Plastics means "able to change its shape freely", and also called synthetic resin in distinction from natural resin (such as rubber and Japanese lacquer). Besides, plastics are also called polymer. It can change its shape freely when molding, and can get hard and turn into stable substrate. Followings are major characteristics and weak points of plastics.
Positive points | Negative points |
---|---|
Difficult to conduct the electricity and heat. Rustless. Hi-impact resistance. Easy to form. Good gloss and colorability. Reasonable and suitable for mass production. |
Easy to break when receive strong pressure. Easy to dissolve to organic solvent. Heat-sensitive, and easy to disintegrate and burn when strongly-heated. Large coefficient of thermal expansion. Easy to generate the static electricity and absorb tiny dust. The application is limited. |
Product technology introduction
Vacuum metalizing
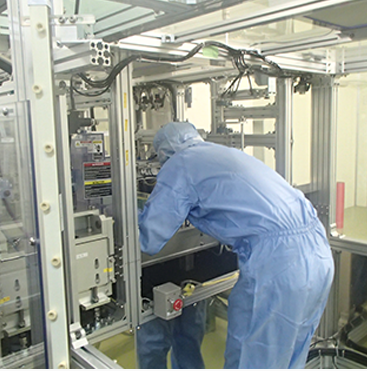
This is the method of vacuum metalizing that evaporating or sublimating the target material by heating to put it on the sheet or film which has low temperature and then make it concentrate. If you heat metal intensively in air, it will be oxidized and crumble. All process is conducted in a vacuum which made by special machine there is no impurity like dust. Also all target material put on the sheet or film with same direction, so it makes its finish smoothly. Any kinds of materials (glass, titanium and so on) can be used for target material.
AS:Anti-static process
Plastic tends to generate static electricity a lot. At MSK antistatic process is applied to some of the products depending on application. This process is widely required for products that are prone to generate static electricity such as front panels for personal computer.
MR:Hard coating process
Plastic is light and tough, but it easily receives scratches on surface and this is one of the weak points. MR process overcome this weak point by enhancing the hardness of the surface. In the optical field, it is used for mobile phone, PDA, TV. In the another field, it is used for expressway windshield, resin glass for cars, glasses, windshield for helmet, and motorcycle windshield etc.
AR:Anti-reflection process
It is not rarely for us to find it difficult to see LC display through the plastic panel because the reflection of plastic occurs.(Reflection ration of each side is 4%.) Anti-reflection process solves this problem and makes the display easier to be seen. MSK AR process is applied to PDA front panels, mobile phone windows, and front-light guiding panels by vacuum metalizing. One of the feature of MSK AR process is improved adhesion technology which was developed through in hard coating process.
Mirror Process (Increased reflection process)
Mirrors are fragile and easy to break in general, but MSK processing metalic layer on plastic surface by vacuum metalizing can make unbreakable mirror. This technology is applied to audio nameplates, ski goggles and helmet wind shield etc. To meet these needs, MSK use vacuum metalizing machine and sputtering machine. Also, we can do special processing which does not block millimeterwave used for car emblems.
Non-glare hard coating process
Non-Glare hard coating is a process that diffuses light by creating irregularity on plastic surfaces. This process cuts dazzle, therefore it is also called anti-dazzle process or light dimming process. Applying this process to front panels of display can reduce the reflection of fluorescent light.
Anti-fog process
As its name suggests, this process prevents the plastic surface from getting clouded. The plastic surface is easy to get clouded, which is one of weak point of plastic and the finding the solution for it has been task for long time. MSK develoved the technology of anti-fog process which has great adhesion to plastic and now it is applied to windshield of helmet.